Experts Reveal Cutting-Edge Solutions for Extreme Conditions
Houston, TX — As demand for dry drilling operations grows in arid regions and environmentally sensitive projects, a critical challenge has emerged: overheating in PDC (Polycrystalline Diamond Compact) drill bits. Without proper cooling systems, these high-performance bits can suffer catastrophic failure. Here’s how industry leaders are tackling the problem.
Why Overheating Happens
In traditional drilling, water or drilling mud cools the bit and removes cuttings. But in dry drilling:
- Friction spikes: PDC cutters generate intense heat when grinding against rock.
- No heat dissipation: Without fluid circulation, temperatures can exceed 800°F (427°C), degrading diamond bonds.
- Dust buildup: Rock particles act as insulators, trapping heat around the bit.
A 2023 study by the Colorado School of Mines found that dry drilling reduces PDC bit lifespan by 50-70% in hard formations like granite.
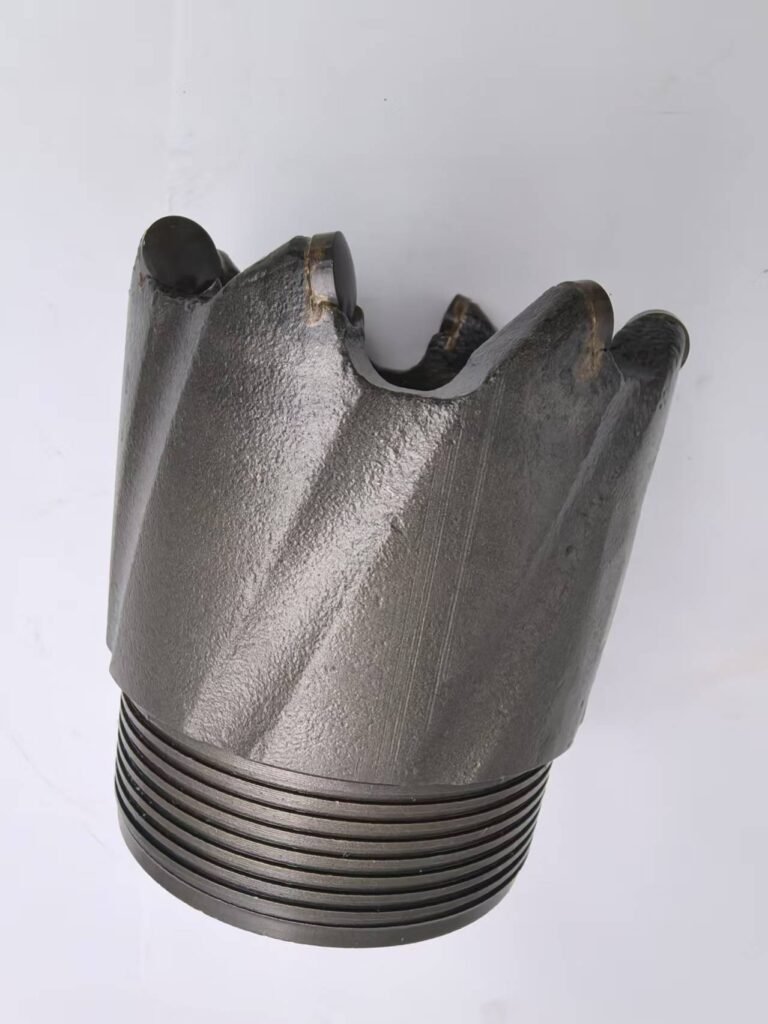
5 Proven Solutions
- Advanced Bit Designs
- Vortex-cooled bits: Use air channels to create cyclonic cooling (e.g., Schlumberger’s “DryFlex” series).
- Thermal barrier coatings: Ceramic layers reflect heat away from cutters (Baker Hughes’ patent-pending tech).
- Smart Drilling Practices
- Pulsed drilling: Intermittent rotation lets bits “rest” and cool.
- Reduced RPMs: Limiting rotation speed cuts friction heat by up to 30% (per Sandvik field tests).
- Alternative Cooling Methods
- Cryogenic air injection: Liquid nitrogen systems tested by NASA for Mars drilling.
- Phase-change materials: Paraffin wax capsules absorb heat as they melt (experimental).
- Material Science Breakthroughs
- Graphene-enhanced cutters: 2D carbon layers improve heat conductivity (Halliburton Lab results show 40% lower temps).
- Self-lubricating matrices: Tungsten carbide with embedded solid lubricants (e.g., molybdenum disulfide).
- AI-Powered Monitoring
- IoT sensors: Real-time temperature alerts via embedded microchips (Varel International’s “SmartBit”).
- Predictive algorithms: AI adjusts drilling parameters before overheating occurs (Shell’s AI trial reduced bit failures by 65%).
Field Test: Success in the Permian Basin
Last month, Occidental Petroleum reported a 22% longer bit life using vortex-cooled PDC bits paired with pulsed drilling in West Texas shale. “It’s about working smarter, not harder,” said site manager Luis Guerrero.
Cost vs. Benefit
While thermal-resistant bits cost 15-20% more upfront, operators save:
- $12,000+/bit in replacement costs (Baker Hughes estimates).
- 3-5 days of downtime per failed bit.
The Future: NASA’s Extreme Testing
With PDC bits slated for lunar missions, NASA’s Extreme Environment Drilling Program is testing diamond-coated bits that can withstand 1,200°F+ (649°C) using laser cooling.
Key Takeaway: “Overheating isn’t a death sentence for dry drilling,” says Dr. Emily Carter, MIT materials scientist. “With the right tech stack, PDC bits can thrive without coolant.”
What’s Next?
- 3D-printed bits with internal cooling labyrinths (Prototyping underway at NOV).
- Bio-inspired designs: Mimicking termite mound ventilation for passive cooling.
🔥 Hot Tip: For real-time overheating diagnostics, check out BitGen’s Thermal Analytics Platform (used by 43% of Fortune 500 drillers).