In the oil and gas industry, selecting the right bit is the key to a successful drilling operation. Different types of drill bits are suitable for different geological conditions, and the wrong choice can lead to inefficiency and even equipment damage. This article will explore several common drill bit types and their application scenarios to help the industry make an informed choice.
- Roller Cone Bits
Cone bits are one of the most common types of bits and are widely used in various geological conditions. Its design features a rotating cone that can effectively break rock. There are two main types of cone bits: steel tooth bits and insert tooth bits.
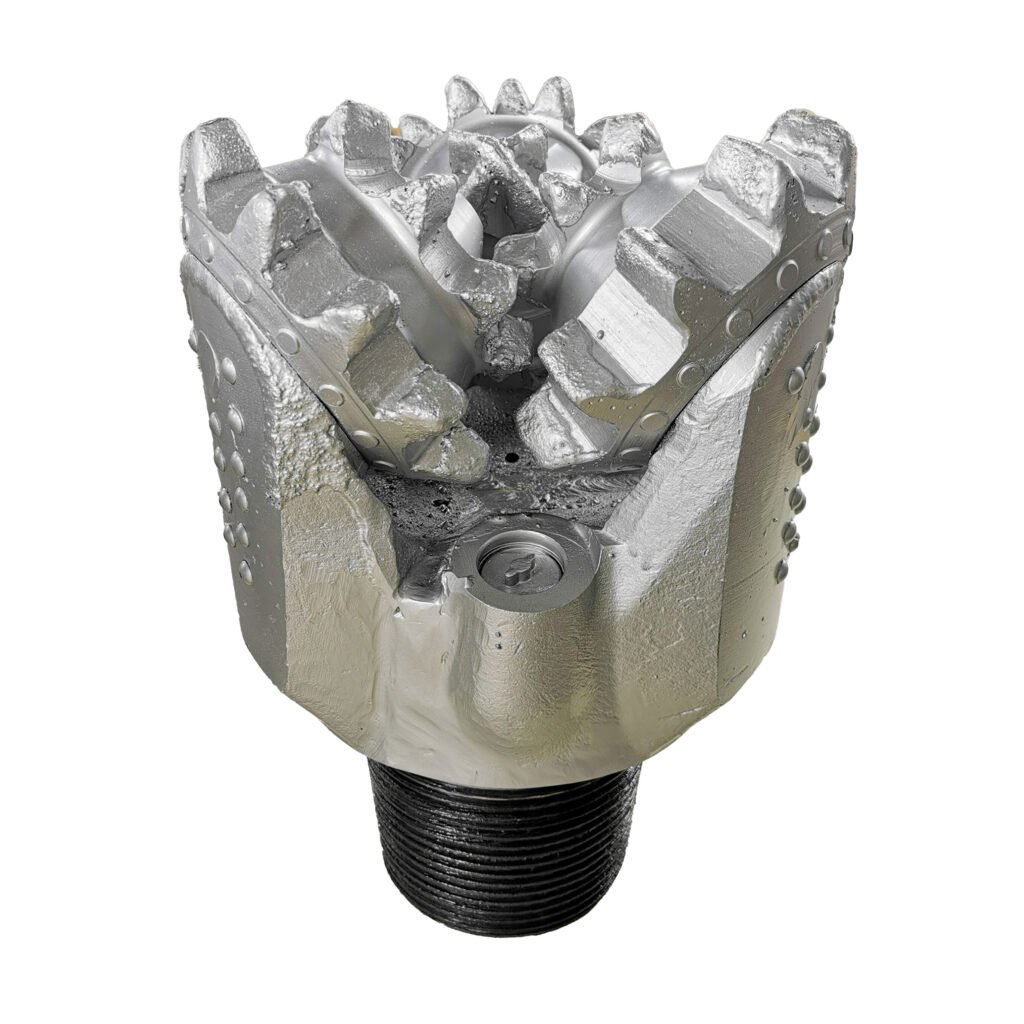
Steel tooth drill bit: Suitable for soft to medium hard formations, such as shale and sandstone. The advantage is that the cost is lower, but the wear in the hard formation is faster.
Insert bit: Suitable for medium to hard formations such as limestone and granite. The teeth of the insert bit are made of cemented carbide, which has better wear resistance but costs more.
- Polycrystalline Diamond Compact Bits (PDC)
PDC bits use polycrystalline diamond as a cutting element and are suitable for soft to medium hard formations. Its advantages are fast drilling speed and long life, but the effect is not good in hard formation. PDC bits have performed well in shale gas and shale oil extraction and have become particularly popular in the North American market in recent years. - Diamond Bits
Diamond bits use natural or synthetic diamond as a cutting element and are suitable for use in extremely hard formations such as granite and quartzite. Its advantages are strong wear resistance and high drilling accuracy, but it is expensive and not suitable for soft formation. - Turbine Bits
The turbine drill is driven by a high-speed rotating turbine and is suitable for deep and ultra-deep well operations. Its advantage is that the drilling speed is fast, but the effect is not good in shallow and medium deep Wells. Turbine drill bits are widely used in offshore drilling platforms.
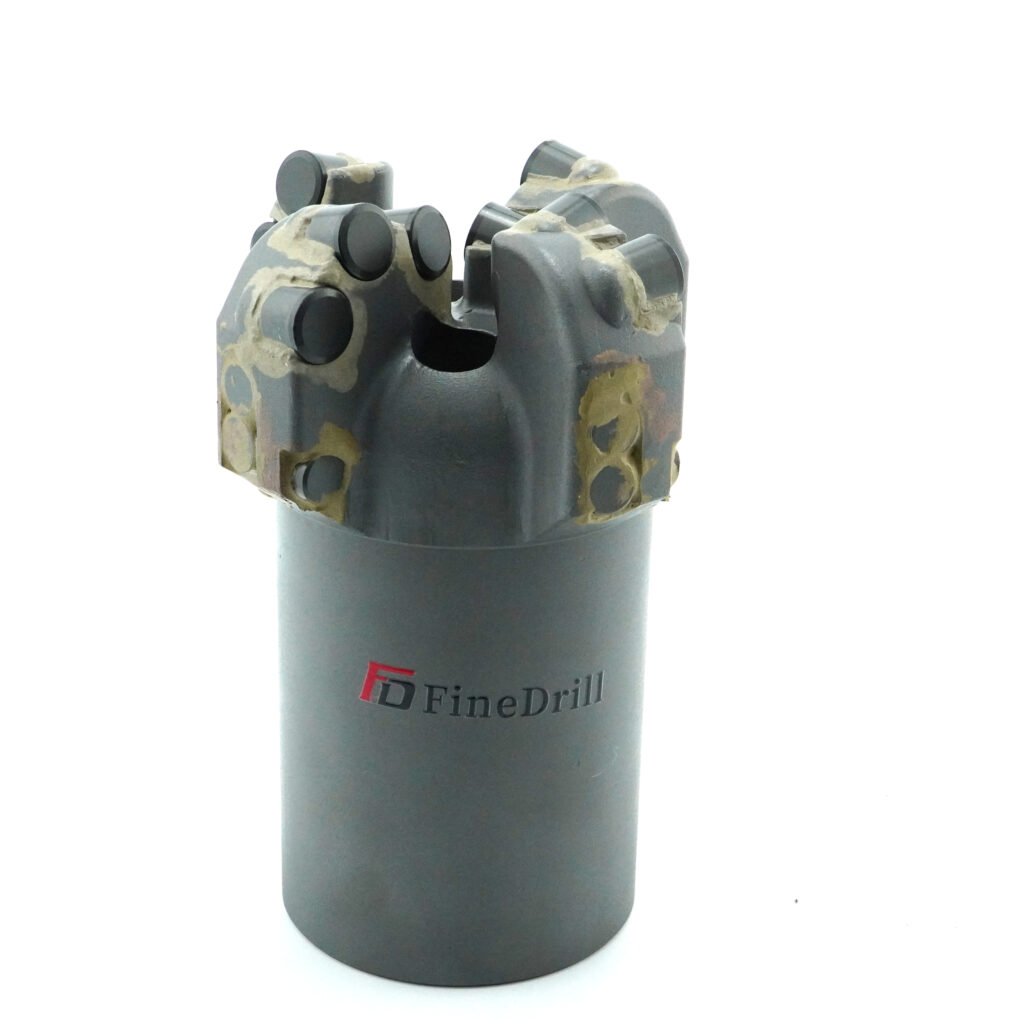
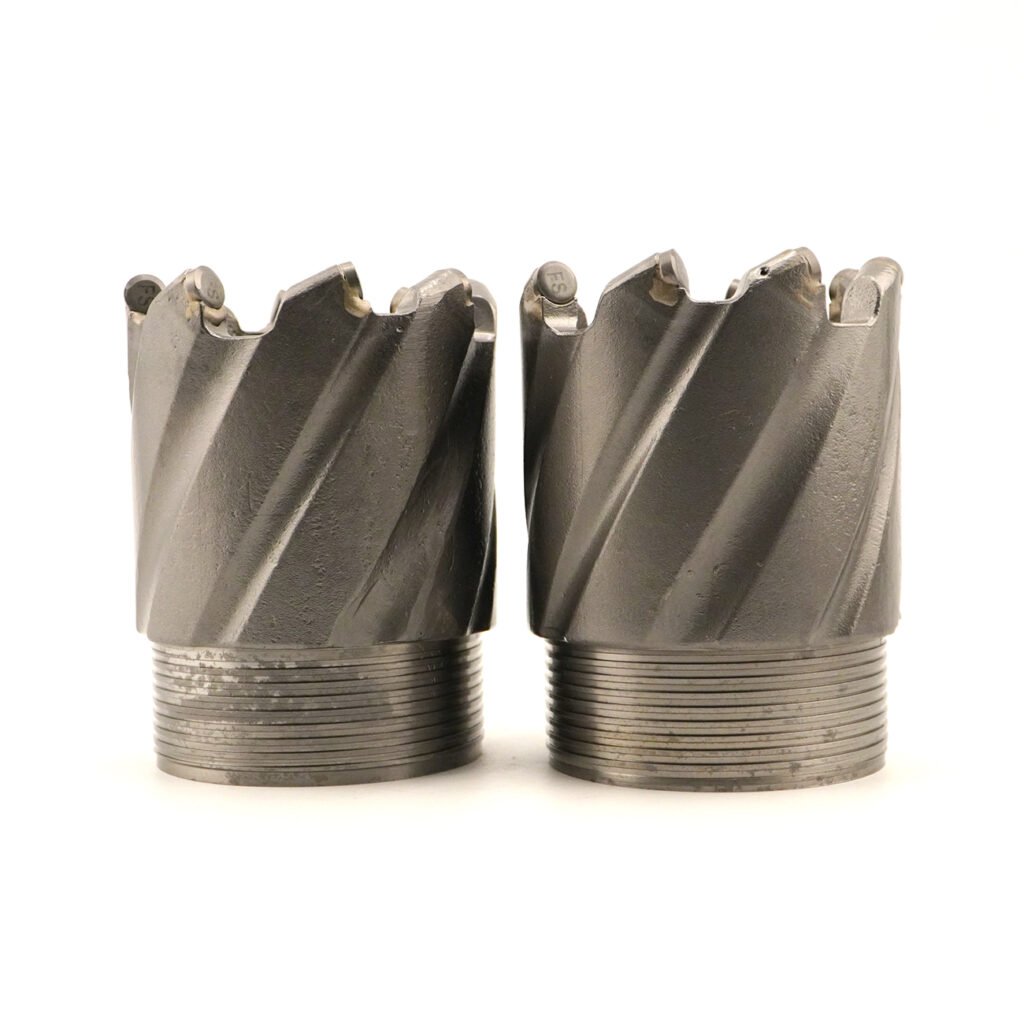
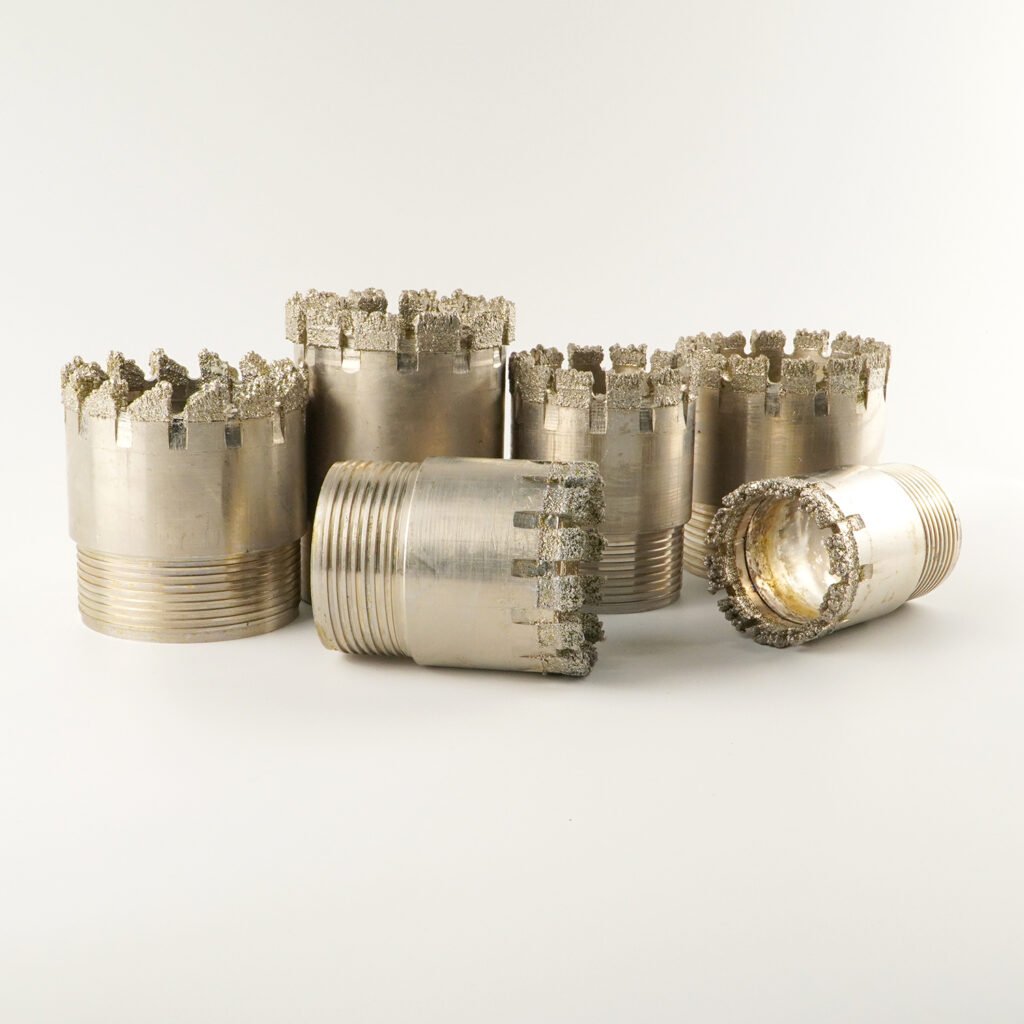
Expert advice
“Choosing the right bit takes into account a number of factors, including formation type, drilling depth, budget and equipment conditions,” said Michael Johnson, principal engineer at the Drilling Technology Institute in Houston. “In practice, we usually conduct formation tests to determine the best type of drill bit.”
conclusion
The success of drilling operations depends on the right bit selection. Cone bits, PDC bits, diamond bits and turbo bits each have their own advantages and disadvantages and are suitable for different geological conditions and drilling needs. Through scientific selection and rational application, drilling companies can significantly improve operational efficiency, reduce costs, and ensure safety.