HOUSTON, TEXAS — As global energy demands push drilling operations into increasingly challenging environments—from shale formations to ultra-deepwater reserves—the question of drill pipe suitability has become a make-or-break factor for project success. Operators are no longer asking, “Will it work?” but rather, “How far can it go?”
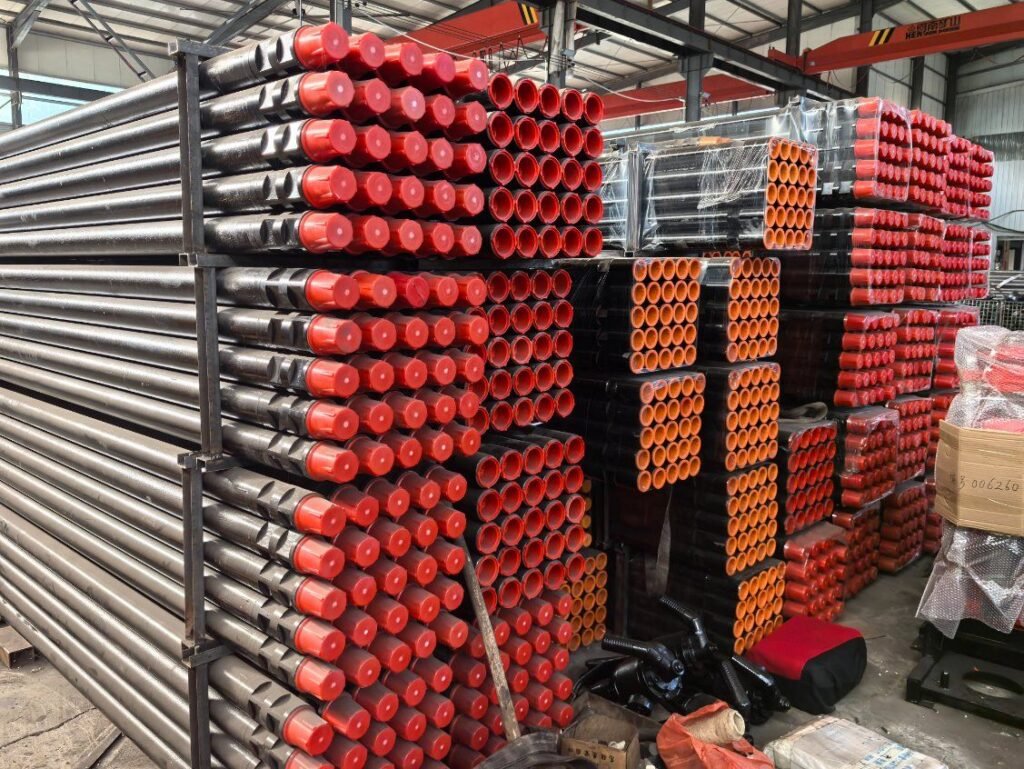
The High-Stakes Game of Material Science
Not all drill pipes are created equal. In shale gas plays like the Permian Basin or Marcellus Formation, where horizontal drilling and multi-stage fracking dominate, pipes face relentless abrasion from lateral friction and cyclic stress. API-grade S135 steel remains a baseline, but operators now demand enhanced wear-resistant coatings (e.g., tungsten carbide) and higher fatigue life to survive 10,000-foot laterals.
“A standard pipe might last six months in shale; our nano-coated variants extend that to 18 months,” claims David Kline, VP of Engineering at DrillTech Solutions. “It’s not just cost—it’s reducing rig downtime.”
Deepwater: Where Pressure and Cold Collide
In deepwater environments like the Gulf of Mexico or Brazil’s pre-salt fields, drill pipes battle pressures exceeding 15,000 psi and temperatures near freezing. Here, material toughness is non-negotiable. Grades like V150 (with superior yield strength) and sour-service alloys (for H₂S resistance) are rising in demand.
But strength isn’t the only hurdle. “Buoyancy becomes a critical design factor,” notes Maria Fernandez, a subsea engineer at TransOcean. “Lightweight yet high-torque pipes are essential to avoid buckling in 10,000-foot water columns.”
Ultra-Deep and Horizontal: The Torture Test
Ultra-deep wells (beyond 30,000 feet) and complex horizontals push pipes to their limits. Torsional stress, differential sticking, and vibration-induced cracks are common killers. Solutions include:
High-torque connections (e.g., double-shoulder designs) to prevent thread galling.
Composite hybrids (steel with carbon fiber segments) to reduce weight while maintaining rigidity.
“We’ve seen pipes snap like twigs in geothermal wells,” warns James Ho, a drilling consultant. “The wrong specs can cost $1M/day in lost circulation.”
The Verdict: Adaptation or Obsolescence
The answer? Yes, drill pipes can handle these extremes—if engineered for the mission. Key takeaways:
Shale: Prioritize abrasion resistance and fatigue life.
Deepwater: Opt for high-yield grades and corrosion-resistant alloys.
Ultra-Deep/Horizontal: Focus on torsional capacity and weight optimization.
As TotalEnergies’ recent $200M pipe order for its Guyana project proves, the market is voting with its wallet. The era of “one-size-fits-all” drill pipe is over.